Research Highlights
Apr. 26, 2024
Improving Polycarbonate's Mechanical Properties Using Fibrous Magnesium Oxysulfate (MOS-HIGE)
1. Background and R&D
Magnesium oxysulfate (MOS-HIGE) is an excellent reinforcing filler for resins. However, when used with polycarbonate (PC), it causes PC hydrolysis, making it difficult to knead and mold. We have developed a technology that prevents PC hydrolysis while enabling resin compositions with highly advanced mechanical properties, such as high flexural modulus and impact strength.
2. MOS-HIGE Characteristics
- Provides high rigidity and flowability* when added to resins (* with lubricant)
- Lighter than common resin reinforcing fillers
- Highly safe due to good solubility in living organisms (solubility in simulated bodily fluid: 0.46 g/L)
- Fine fibers create smooth resin molded surfaces
- Low Mohs hardness extends mold life
MOS-HIGE Manufacturing Flow
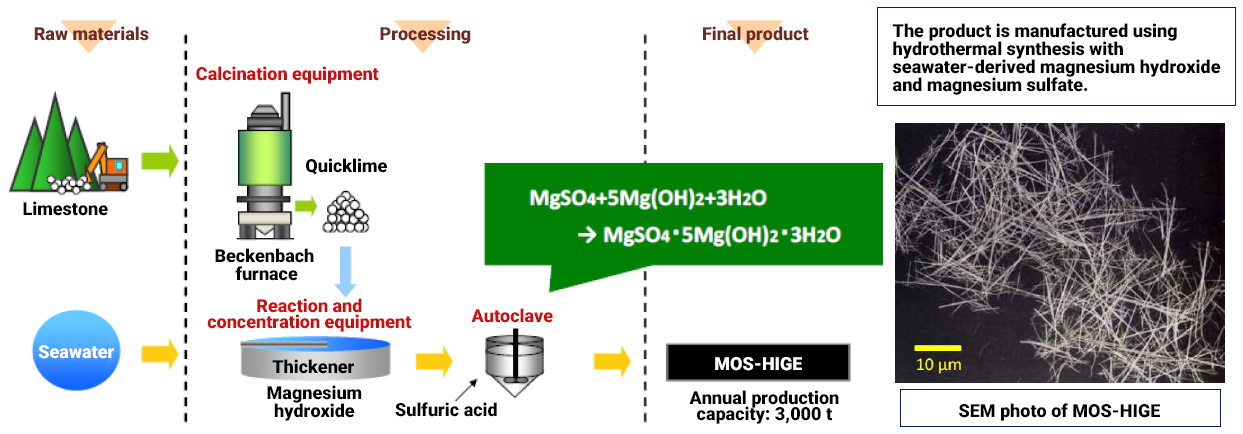
Comparison of Properties with Other Inorganic Fillers
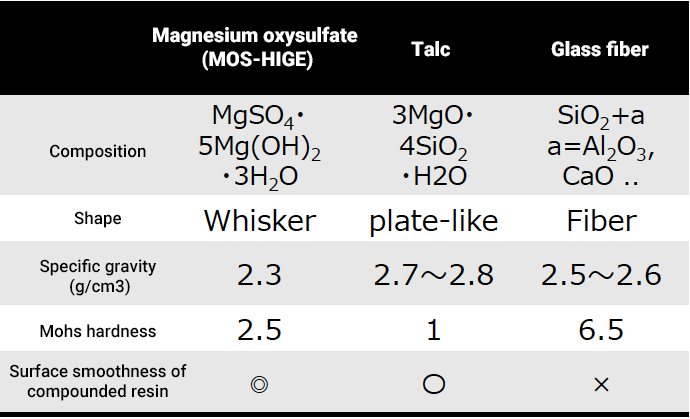
Benefits of MOS-HIGE for Polypropylene
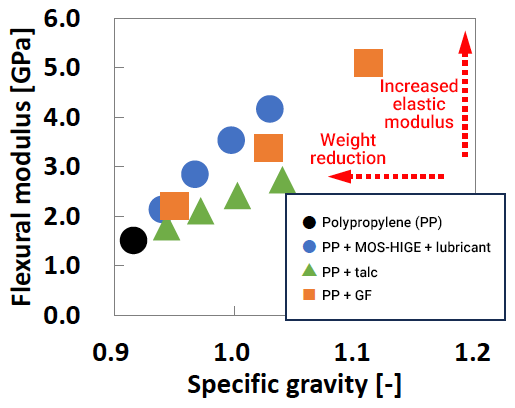
3. Main Applications of MOS-HIGE
- Automotive PP (resin reinforcement)
- Gaskets and packings (wear resistance)
- Flame retardant additive
- Paints and adhesives (thickening, thixotropy)
- Rubber (anti-slip properties)
- Asbestos replacement
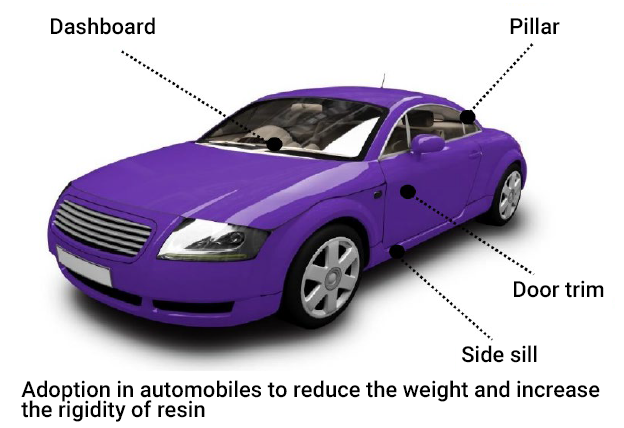
4. Developed Technology and Benefits of MOS-HIGE for Polycarbonate (PC) Relationship between Modifier Content and Resin Properties in PC/MOS-HIGE-MB and PC/GF-MB
Developed Technology
- Pre-mix MOS-HIGE, PP, lubricant, and new modifier to create a master batch
- Mix the master batch with PC and pelletize
Benefits for PC
- Improved flexural modulus compared to PC alone
- Reduced PC hydrolysis
- Improved impact strength

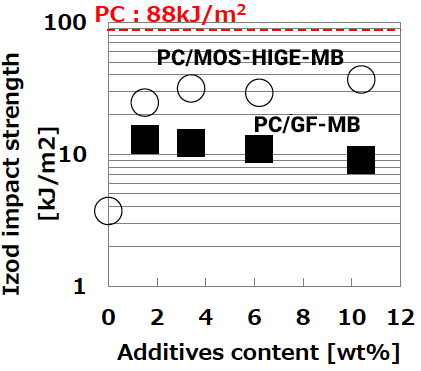
5. Proposed Mechanism
(1) Reduced PC hydrolysis
Through the master batch method and lubricant effect, MOS-HIGE localizes in PP, and adding a new modifier forms a modifier layer between PP and PC. This microstructure reduces contact between PC and MOS-HIGE, reducing PC hydrolysis and improving impact strength.
(2) Improved impact strength
Changes in the fracture mechanism, verified during impact testing, significantly affect impact strength. The diagram below shows the expected changes in the fracture mechanism with modifier addition.
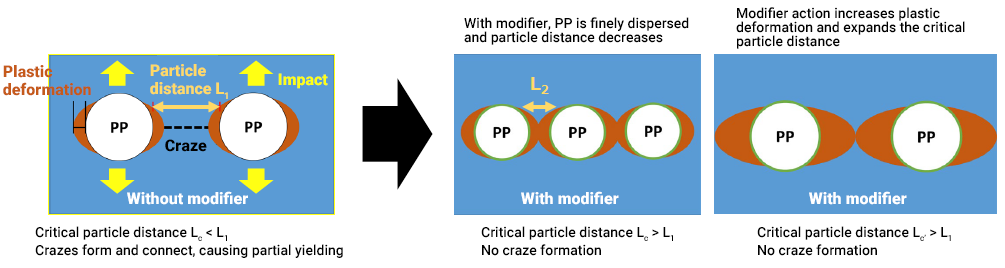
With modifier addition, the distance between PP particles becomes less than the critical particle distance, and the fracture mechanism changes from small-scale yielding to full cross-section yielding, which is believed to improve impact strength.
6. References
31st Autumn Conference of the Japan Society of Polymer Processing, P-009
Patent No. 6747694
Back numbers
- Nov. 1, 2023
- Accelerating Development Using Data Science